New Products
Linear AMC Module Production System *AMC: Automated Material Connect
- Propose Coating Process for various Resin Materials such as Optical Bonding Materials as One-stop Solution.
- Realized Lower Cost Process by optimizing Module Production Process with Circulation Linear Transport System.
-
Enabled to link with applications such as High-Precision Coating Mechanism like Ink-Jet Printer, Dispenser, etc.
in accordance with the production sites. System Upgrading with Laminator / Assembling Mechanism is possible. - Applications: Module Process for Information Terminals such as Smartphone and Tablet, Information Display Devices such as In-Vehicle Center Information Display, and Various Coating and Assembling Process
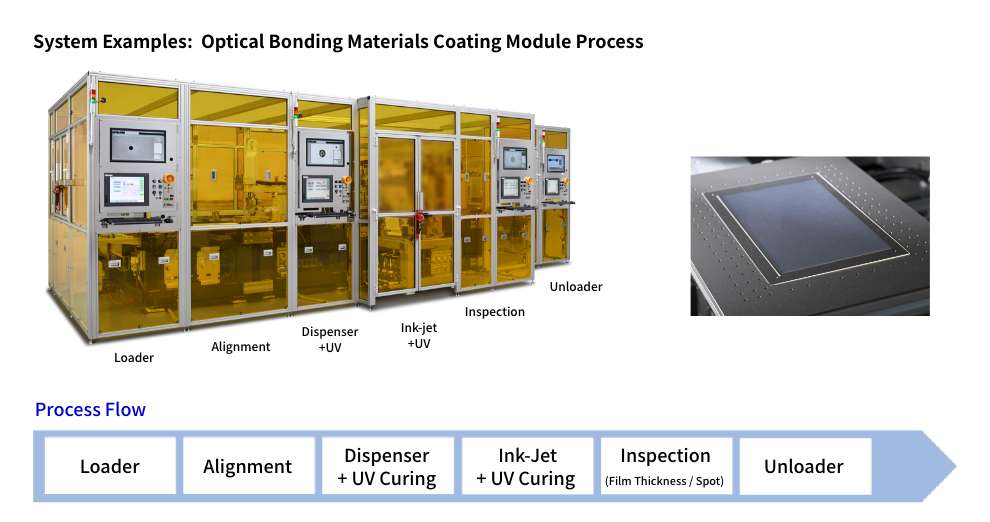
No. | Items | Specifications |
---|---|---|
1 | Work Size | 340mm×250mm |
2 | Work Materials |
Alkali-free Glass / Glass Epoxy Please inquire for details. |
3 | Applicable Materials |
Optical Bonding Materials, etc. Please inquire for details. |
4 | Line Cycle Time |
12sec. & over Varied depending on System Configuration |
5 | System Upgrading | Refer to System Upgrading Mechanism at the right column. |
6 | System Size |
W8,200 x D3,200 x H2,400mm Varied depending on System Configuration |
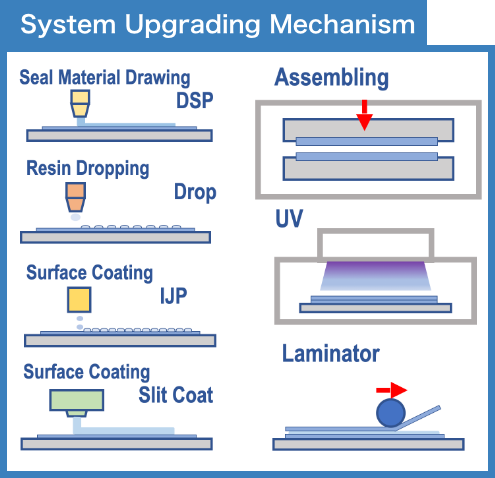
Solder Ball Mounter for Wafer
- Realized Higher Yield by applying Ball Mounting Technology for Semiconductor Package Substrate to Wafer
- Enabled High Quality & Stable Production by Special Flux Printing Technology
- Improved Productivity by New Squeegee Head
- Compact Design
- Applicable for SECS/GEM, OHT & AGV (Option)
Features
-
Flux Printing
・Reduced Flux Bleeding by Gap Printing
・Stabled Transfer Position by One-direction Printing Mechanism
・Minimized Cleaning Frequency -
Ball Mounting
・New Infinity Head (Triple Type Rotary & Closed Type Squeegee)
・Higher Throughput
・Minimized Sweeping Frequency
(1/3 compared with the conventional type)
・ Increased Solder Ball Use Efficiency
(1/2 compared with the conventional type)
Application
- Wafer such as WLCSP, FOWLP, etc.
Inspection & Repair
- Enabled to systematize Ball Mounting System with Inspection & Repair Equipment
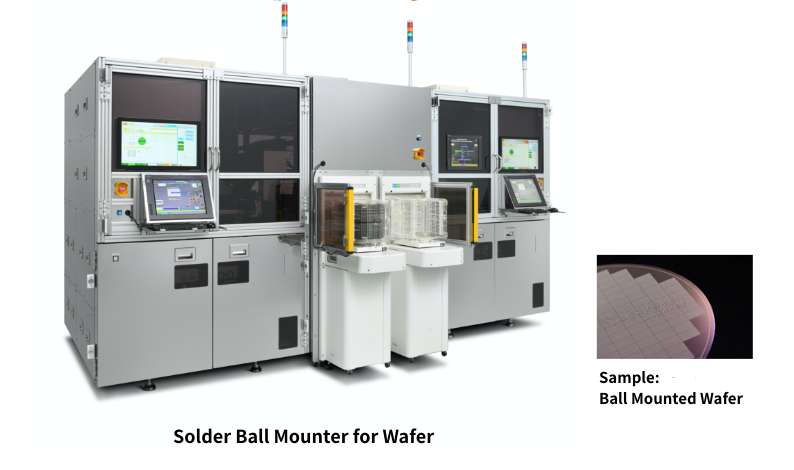
No. | Items | Specifications | |
---|---|---|---|
ABM-04G-WFS | ABM-04S-WFS | ||
1 | Wafer Size | Φ300mm Φ200mm |
Φ300mm Φ200mm |
2 | Handling System | Load port (FOUP or FOSB) |
Load port (FOUP or FOSB) |
3 | Applicable Ball Size | 40um~300um | 80um~300um |
4 | Alignment Accuracy | <±10um | <±15um |
5 | Flux Printing |
Gap Printing (Single Direction) |
Gap Printing (Single Direction) |
6 | Ball Mounting | Adopted New Infinity Head (Triple Type Rotary & Closed Type Squeegee) | Adopted New Infinity Head (Triple Type Rotary & Closed Type Squeegee) |
7 | Ball Missing Rate | <20ppm (as per AIM’s test conditions) |
<30ppm (as per AIM’s test conditions) |
8 | Throughput |
65UPH (as per AIM’s test conditions) |
40UPH (as per AIM’s test conditions) |
9 | Equipment Size | 3995(W)x2150(D)x2020(H)mm | 3555(W)x2150(D)x2020(H)mm |
10 | Equipment Weight | Approx. 3,500kg | Approx. 3,300kg |
Φ30um Solder Ball Mounting System (Patented)
- Realized Uniform Flux Coating enabling Ultra Fine Pitch by Inkjet Technology.
- Contributed to Stable Ball Mounting and Productivity Improvement by High-Speed Rotary Head.
- Enabled High-Speed Inspection and Repair by “On the Fly Inspection” as Non-Stop Continuous Inspection.
- Total Solution contributing to Yield and Productivity Improvement for Microscopic Solder Ball Mounting Process with Ultra Fine Pitch.
Features
-
Flux Coating
Inkjet Coating without using conventional Stencil Mask -
Ball Mounting
New Rotary Head to provide High Throughput -
Inspection & Repair
Continuous High-Speed Inspection (On the Fly)
Capable for □120mm Unit size Inspection & Repair - Not required Stencil mask for Flux printing process and Flux Usage to be improved
Application
-
Package Substrate
(FCCSP, FCBGA, MCP/MPU, 2.5/3D, FOPLP, etc.) - Wafer (WLCSP, FOWLP, etc.)
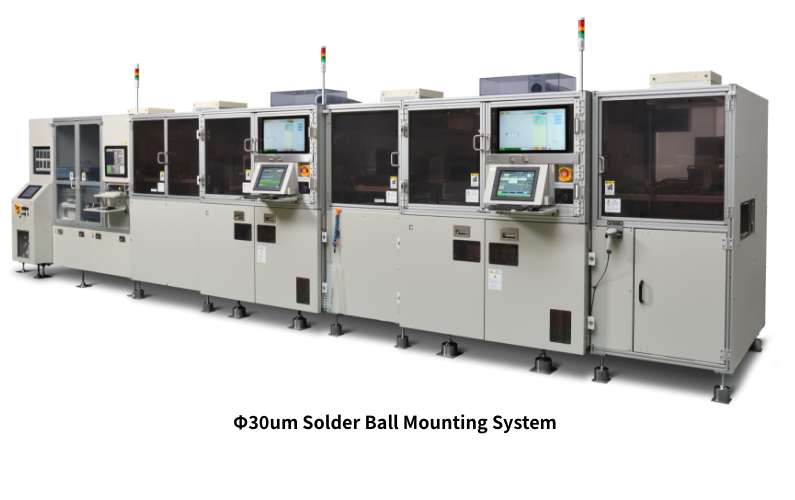
No. | Items | Specifications |
---|---|---|
1 | Work Size |
Substrate: Max. 340L×250W (mm) Wafer: Max.12“ (φ300mm) |
2 | Work Type | Substrate Wafer for Package like Substrate Epoxy Glass, etc. |
3 | Applied Ball Diameter | 30um - 300um |
4 | Flux Coating Equipment | Inkjet Coating |
5 | Solder Ball Mounting Equipment |
High-Speed Ball Mounting, No Ball: 30ppm (AIM’s conditions) |
6 | Inspection Method |
On the Fly Inspection Max. Unit Size □120mm |
7 | Throughput | 65UPH (AIM’s conditions) |
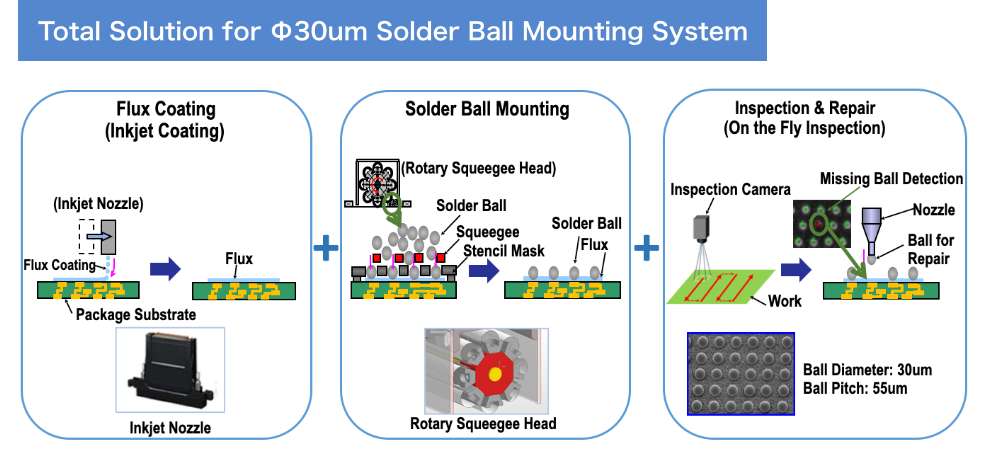
Plasma Laser Repair Equipment ALR-04G-P4 (PAT. PEND.)
- Plasma Laser Repair Equipment for Semiconductor Packages enabling Yield Improvement
- Enabled Inspection and Repair for Solder Ball Drop Defects during Reflow and De-Flux Cleaning Process after Ball Mounting
- Realized Spot Reflow soldering (local soldering for only repairing points) by integrating Plasma and Laser Technologies
- Minimized Reflow Process impacting qualities of Semiconductor Packages
Features
- Realized Inspection & Repair for Ball Drop Defects during Reflow and Cleaning Process
- High Speed Overall Surface Inspection for Work(Substrate and Wafer)
- Flux dipping & High Precision Solder Ball Mounting
- Soldering by Plasma & Laser technologies
- Proposal for Off-Line or In-Line System
Application
-
Package Substrate & Unit Substrate after Dividing
(FCCSP, FCBGA, MCP/MPU, 2.5/3D, FOPLP, etc.) - Wafer (WLCSP, FOWLP, etc.)
No. | Items | Specifications |
---|---|---|
1 | Work Size |
Substrate: Max. 340L×250W (mm) Wafer: Max.12“ (φ300mm) |
2 | Work Type | Substrate (Epoxy Glass, etc.) Wafer |
3 | Applied Ball Diameter | 40um - 300um |
4 | Inspection Method | On the Fly Inspection |
5 | Solder Ball soldering Method | Plasma + Laser |
6 | Cycle Time (Repair + Solder Ball soldering) | 50 sec. (based on our conditions for evaluation) |
7 | Equipment Dimensions |
W2,600 x D2,400 x H2,150mm (excl. Handling & Projected Portion) |
8 | Equipment Weight | 3,000 kg |
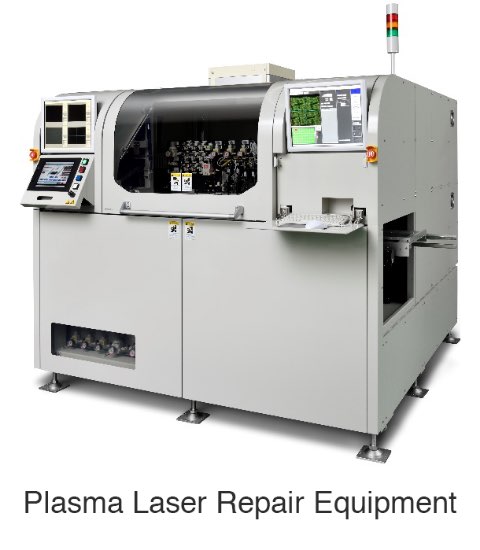
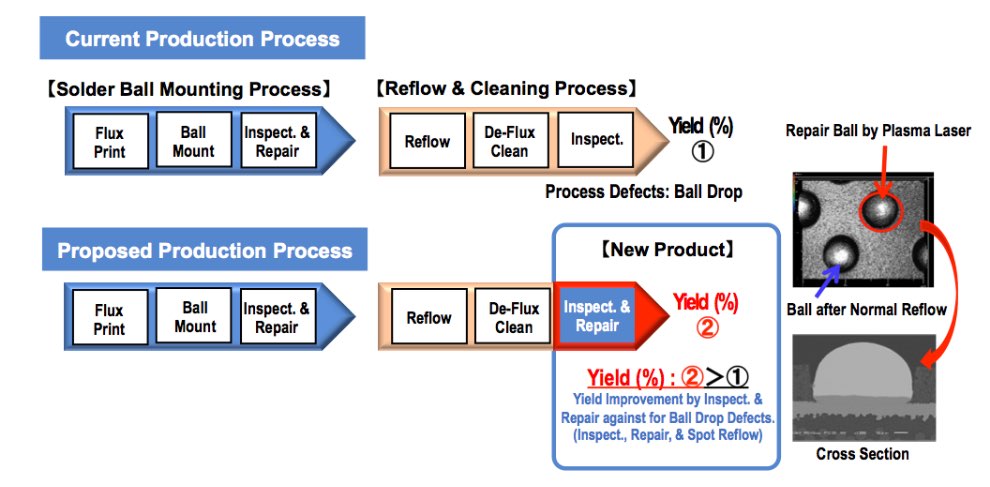
Nano-level High Precision Vacuum Assembling System (NPV-300))
- High Precision Vacuum Assembling System enabling Nano-level Assembling Precision
- Improved Device Performance by integrating with Ink-jet Microscopic High Precision Coating Technology
- Propose One Stop Solution by which contribute to improve Manufacturing Process and Production Efficiency
Features
- Higher Precision was realized by newly developed Nano-level Alignment Mechanism
- Improved Resolution by Higher Resolution Camera
- External Micro-vibration Control by Vibration Isolation Control System (Option)
Application
- Micro Display (Micro LED, Si-OLED XR (AR/VR/MR), LCOS, HTPS)
- Optical Device (CMOS, Various Sensors)
- Sensing Device (LiDAR)
No. | Items | Specifications |
---|---|---|
1 | Work Size |
8”(φ200mm) 12“(φ300mm) |
2 | Work Materials | Alkali-free Glass / Si |
3 | Work Holding Method | D-PSC / LVC Method |
4 | Assembling Accuracy | ≦100nm |
5 | Assembling Load | 0.5KN(Max) |
6 | Vacuum Degree | < 10-1Pa |
7 | Equipment Size | W2,800 × D2.400 × H2,900mm |
8 | Equipment Weight | 7,000kg |
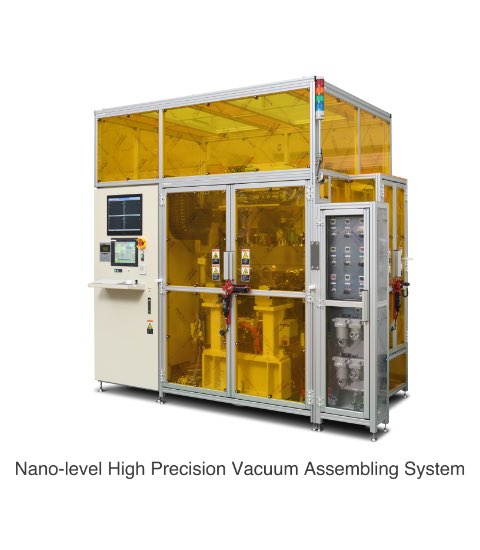
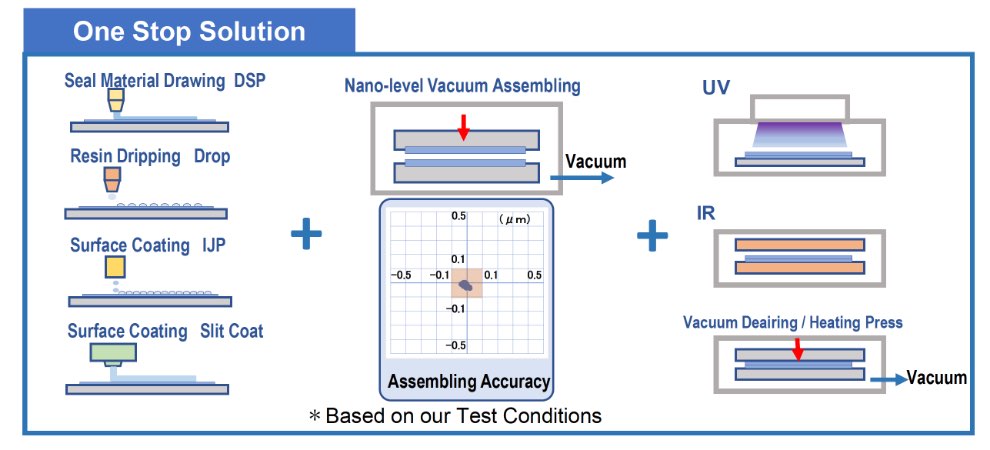
RGB Ink-Jet Printing System
- Capable for forming materials of OLED, QDOLED and QDμLED, etc.
- Supplied many process equipment and control system for large panels’ field
- Turnkey solution (Ink-jet Printing, Dry, Bake, Environment)
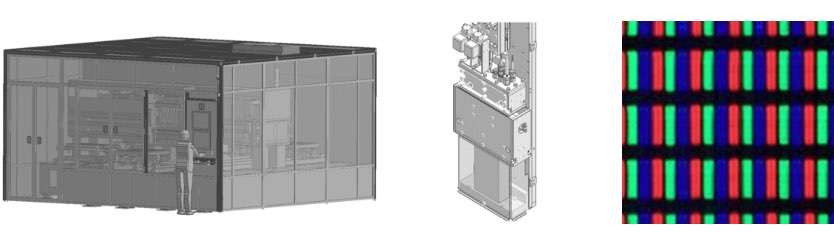
Use optimum nozzles for materials characteristics
- Material circulation mechanism for QD forming materials and accurate temperature control
- Optimize wave form by intelligent ink-jet head and controller
Mass-production technology standard equipped
- Matrix offset and injecting pitch (liquid-droplets’ pitch) offset
- High speed inspection for all Nozzles injection and dripped volume & position
- Minimize idle time by simultaneous calibration mechanism and structure
Optimize vacuum dry process
- Optimum design and construction by vacuum control technology and numerical analysis
- Liquid analysis, VCD vacuum dry, Liquid-droplets behavior simulation
Applicable for various pixel design
- Pen tile, Side by side and Line bank
Solder Ball Mounter
- Ensure and deliver mass-production by 40um solder ball
- New rotary head provides high throughput (25% improved vs Conventional head)
- On the fly inspection is capable for large packages without any limitation.
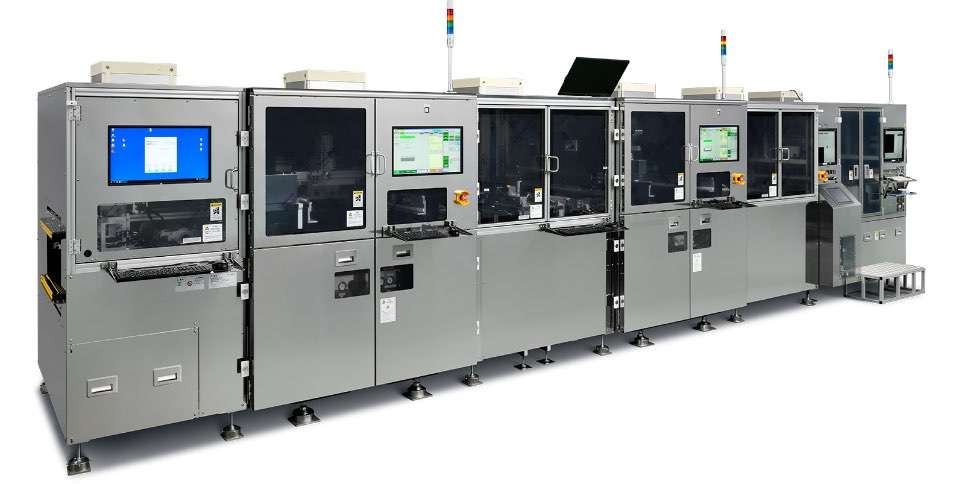
Items | Specifications |
---|---|
Line Configuration | Flux / Ball printer / Inspection & Repair |
Panel Transportation | Pick & Place (Vacuum pad) or Pick & Place (Clamp) |
Throughput(Tact Time) | 65sec |
Applicable panel size | Max. 420 x 300 - Min. 200L x 75W(mm) |
Applicable ball diameter | 40 - 500(μm) |
Alignment repeatability | < ±10um |
Missing rate (No ball ratio) | < 20ppm |
Inspection method | On the fly inspection (Non-stop imaging) |
Applicable max. unit size | 120.0 × 120.0(mm) |
Inspection time (Reference) | Approx 16sec./ 1/4 panel(144unit/panel) |
Repair | With Flux W/O Flux Available |
Ball remove (for extra ball) | Available |
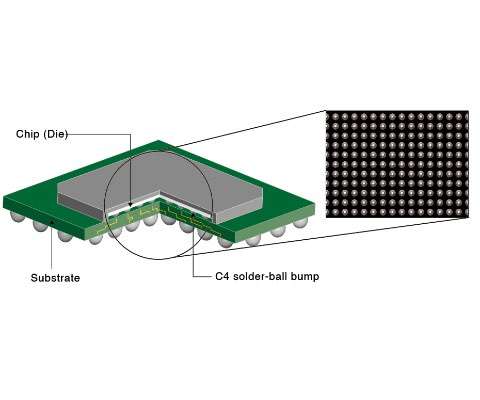
Micro Display Production System
- Turnkey ODF solution for 200mm and 300mm Wafer
- Deliver high performed gap control and ensure high productivity
- Contributing to various micro display production now (OLED,LCOS,HTPS)
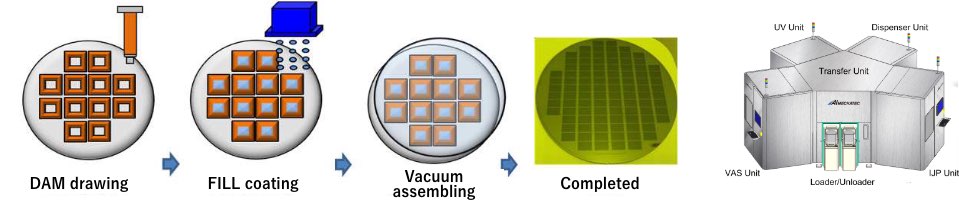
Turnkey Solution
- High yield
- Quick set-up & Sable mass-production
- Process supports by own know-how
All in One System
-
DAM drawing Dispenser
High speed & Fine line drawing (600um -
FILL coating Ink-Jet
Capable for High viscosity material (~1000mPa/s) -
VAS (Vacuum Assembling System)
High accurate assembling (Accuracy: 3σ≦0.2um)
Smart Production System
- Capable system for factory automated production & Remote supports system
- Integrated control for process equipment and material supply system
- Provide a solution for clean environment and products

System integrated Control & Management
- Remote
- Optimal process
- Energy saving
- Maintenance & Service
Automation 1
(for Process Equipment)
- Material supply
- Set-up for products changeover
Automation 2
(for Transport System & Unit)
- Transport system
- Set-up for materials preparation
-
Set Up for materials preparation (Example) -
Transport system(Example) -
Set Up for production changeover(Example)